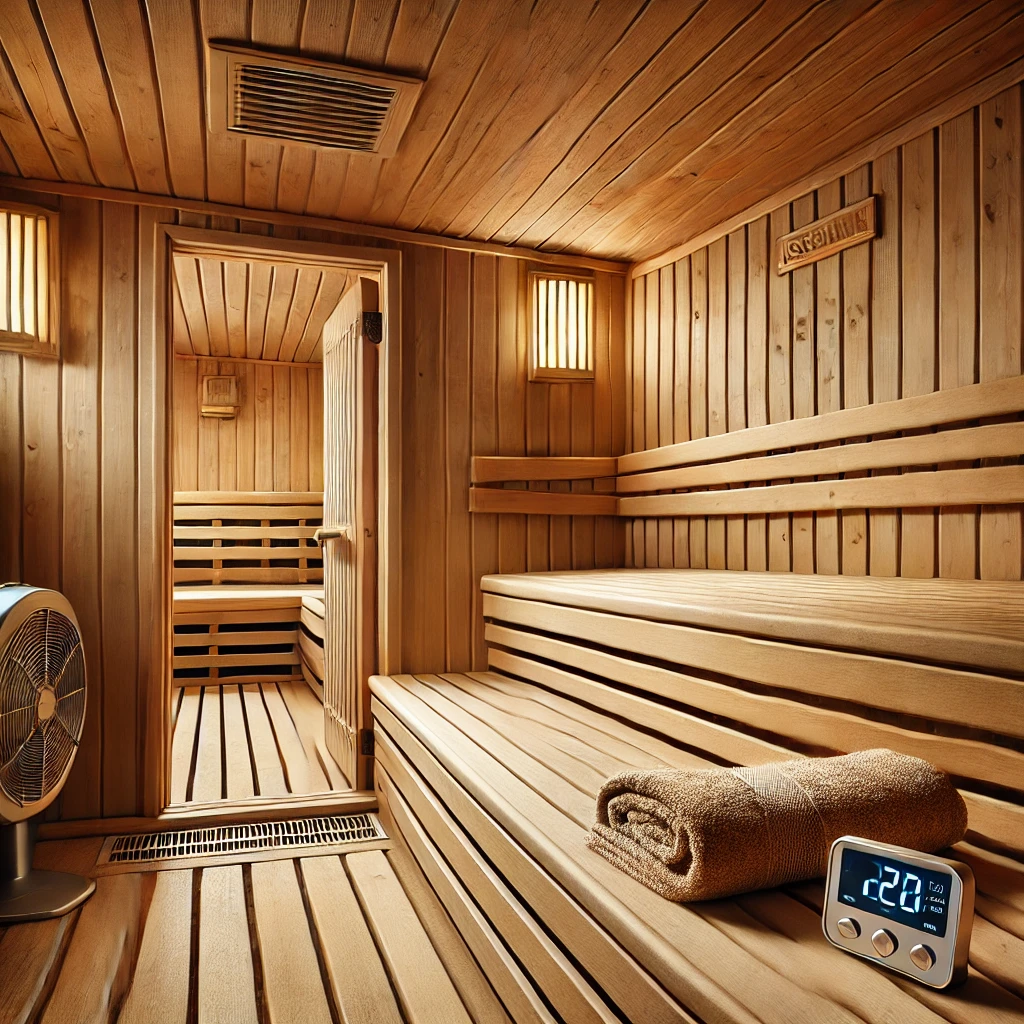
Mold and moisture are among the most common threats to both traditional and infrared saunas. Persistent humidity, poor ventilation, and inadequate cleaning create ideal conditions for microbial growth. These issues can compromise wood surfaces, degrade equipment, and pose health risks. Preventing mold and moisture buildup requires a disciplined approach to ventilation, surface hygiene, humidity monitoring, and structural design.
Understanding the Risks of Moisture and Mold in Saunas
Moist environments like saunas promote microbial proliferation when not properly managed. The constant cycle of heat and cooling increases the potential for condensation, especially in enclosed spaces.
Key problems include:
- Wood rot and warping from saturated surfaces
- Fungal growth in bench joints, floorboards, and under seating
- Airborne spores, contributing to respiratory irritation
- Degradation of insulation and wiring in electric heater systems
Addressing these risks is essential for safety, hygiene, and long-term structural preservation.
The Role of Ventilation in Mold Prevention
Proper ventilation is the first line of defense against excess humidity and stagnant air.
Recommended airflow setup:
- Intake vent: Located low on the wall near the heater to introduce fresh air.
- Exhaust vent: High on the opposite wall to release humid air and steam.
- Maintain continuous air exchange during and after sessions.
- For infrared units, natural or mechanical ventilation should still be present even without steam.
Ventilation must remain unobstructed at all times. In commercial environments, an active exhaust fan may be required for sufficient air turnover.
Daily Drying Protocols After Each Use
Routine drying is essential to prevent excess condensation and mold development.
Post-use protocol:
- Leave the door open for at least 30–60 minutes after each session.
- Remove damp towels, mats, or seat covers immediately.
- Wipe down benches and walls with a dry cloth or mop to eliminate standing moisture.
- Ensure ambient room temperature supports fast evaporation.
Use a small floor fan if necessary to expedite drying, particularly in humid climates or basements.
Wood Material Considerations and Water Resistance
Different wood species respond differently to prolonged exposure. Most imported saunas use Hemlock, Cedar, or Spruce, all of which offer decent natural resistance to moisture.
Best practices:
- Never apply sealants, stains, or oils to interior wood.
- Sand surfaces lightly every 6–12 months to refresh pores and remove residue.
- Inspect for softening, darkening, or mildew odor, especially in joints and lower surfaces.
Use only non-toxic cleaning products to avoid residue buildup that can trap moisture or feed mold spores.
Monitoring Humidity and Condensation
Track humidity with a digital hygrometer to maintain optimal environmental conditions.
- Ideal humidity level after use: below 50%
- During use: Up to 60–70% for traditional models, 30–40% for infrared
- Use desiccant containers or commercial-grade dehumidifiers in high-humidity zones
Infrared saunas often accumulate hidden moisture from sweat vapor, requiring as much humidity control as steam-based systems.
Deep Cleaning Strategies for Mold Prevention
In addition to daily drying, implement a consistent deep-cleaning schedule.
Monthly mold prevention checklist:
- Wipe all wood surfaces with a 50:50 vinegar and water solution.
- Clean under benches and removable floor slats with a soft-bristle brush.
- Inspect heater stones and replace if blackened or developing odor.
- Use a UV sterilizing light periodically in commercial environments to destroy microbial residues.
Never use bleach or ammonia, which can release harmful vapors when heated and damage the wood.
Design and Environmental Planning
Structural design impacts moisture management more than any other variable. Key architectural considerations include:
- Use vapor barriers in walls and ceilings behind sauna paneling to prevent moisture seepage.
- Install non-porous flooring outside the sauna entrance to reduce tracking of moisture.
- Elevate the sauna slightly off the floor if in a basement or near water-prone areas.
- Consider glass doors that promote airflow when open and are resistant to mold.
Outdoor saunas should include roof overhangs, weatherproof flashing, and gutter systems to prevent rainwater intrusion.
When Mold Appears: Remediation Steps
If mold becomes visible or detected through odor:
- Remove and isolate affected materials if possible (e.g., floor mats, trim).
- Clean surfaces with hydrogen peroxide-based spray (3% solution) or vinegar.
- Use a dehumidifier continuously for 48–72 hours post-cleaning.
- If wood is structurally compromised, replace affected planks and check insulation behind paneling.
- Consult a professional mold remediation expert if mold persists despite cleaning.
Early detection prevents the need for costly rebuilds or full interior panel replacement.
Commercial Sauna Mold Prevention Protocols
High-traffic wellness facilities must implement stricter mold control due to the volume of users and condensation cycles.
Best practices include:
- Logging daily ventilation and drying tasks
- Cleaning with approved sanitizers after every use window
- Installing high-capacity HVAC exhaust systems
- Scheduling quarterly professional inspections of all moisture-prone surfaces
Lack of compliance in commercial environments can result in health code violations and liability claims.
Long-Term Impact of Moisture Control
Effective moisture and mold management results in:
- Extended wood and heater lifespan
- Improved air quality and guest safety
- Reduced energy costs from efficient drying cycles
- Fewer structural repairs or replacements over time
Integrating these practices ensures your sauna remains not only functional but also hygienic and inviting for years to come.